Products Used | Trac-Mount™ Idler |
---|---|
Product Types Used | Transfer Point Solutions , Belt Support |
Industry | Mining |
Customer | PT Antan Nickel Mining, Southeast Sulawesi, Indonesia |
Problem

PT Antam Nickel Mining of Indonesia was experiencing excessive equipment wear and damage at a main transfer point leading from the rotary dryer, handling 64,800 tonnes (71,430 tons) per month of bulk material. The impact force of cargo on an unsupported belt was cracking idlers and bending the mainframe. The damage forced operators to shut down the entire system regularly to repair mainframe damage and replace broken equipment. Several times the mainframe directly below the transfer point needed to be replaced, an expensive and labor intensive project. New equipment, increased labor and lost production were costing the company thousands of dollars annually. Managers sought out solutions to bolster production and profitability.
Solution

Technicians from PT. Suprabakti Mandiri, distributor of Martin Engineering equipment in Indonesia, examined the issue and determined that the support system of the loading zone could be improved with more robust and updated technology. A Martin® Impact Cradle MD and Martin® Slider Cradle were installed, along with Martin® Trac-Mount™ Idlers in between each cradle to avoid pinch points and maintain a consistent tough angle. Able to absorb up to 8500 pounds (3856 kg) of force, the Martin® Impact Cradle MD protects the mainframe and reduces damage to the belt, while the Martin® Slider Cradle centers the load and creates a smooth path through the settling zone. Working in tandem, these components improve the efficiency of bulk transfer, reduce off-center cargo and increase system performance.
Results

Upon the six-week inspection, Martin Supra representatives found that the equipment met or exceeded operators' expectations. "There has been zero damage to the system, mainframe or components since the installation," plant managers revealed. "Production is smoother and we've experienced a noticeable increase." Downtime due to equipment failure has been significantly reduced in the problem area. The new components are projected to have a positive influence on the plant's cost of labor, annual equipment expenditures and overall cost of operation, providing an excellent return on investment.
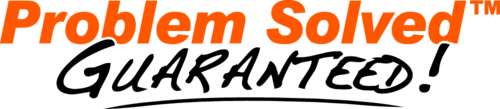
We've solved your problem somewhere before!
While your problem seems unique and frustrating, with 70+ years of solving similar problems around the world, and with the most experienced and educated people on our teams, we can assure you that we’ve “Been There, Done That.” At least close enough to know what needs to be done next and adjust for your situation.
Put Us To The Test For Free! Let Us Give You a Solution.