Increase profitability and productivity by reducing downtime.
Every second that your plant is down it costs you money because output stops. Whether you’re transporting coal to a power plant, removing material from an underground mine, unloading freight from a cargo ship or manufacturing products on an assembly line, you’re productive only when the equipment is running smoothly.
Because there are so many moving parts, it doesn’t take much to cause a shutdown. Material can spill from the belt and accumulate below or get carried back on the return strand. Carryback can cause the most critical component of the entire system, the conveyor belt, to fall out of alignment and suffer severe edge damage. Bulk solids can also build up inside chutes and hoppers, reducing flow, particularly in high-moisture environments. These bottlenecks can happen anywhere in the process.
Another source of unscheduled downtime is when the potential risk of injury or illness exists. For example, when the fugitive dust becomes airborne and causes a potentially explosive environment, the process must be shut down and the risk remediated.
If your operation is experiencing unscheduled downtime, talk to one of our experts. We’re standing ready to listen to you describe your operation and offer recommendations on how to reduce shutdowns at your plant. Our team is available to provide expert advice and assistance on all of your bulk material handling questions and problems.
Sonic Horn Eliminates Downtime From Ash Accumulation
Belt Cleaners Save Copper Mine $22,000 Per Week In Downtime
Cement Plants Puts An End To Unscheduled Downtime With Martin Products
Belt Cleaners Reduce Downtime And Improve Safety
Transfer Point Solutions Solve Fugitive Cargo Issues
Chute Structure Products Reduce Unscheduled Downtime
CleanScrape® Cleaner Improves Operations At Rock Quarry
Martin® Belt Cleaners Minimize Downtime For Cleanup
Chute Clogging And Spillage Corrected With CleanScrape® Cleaner
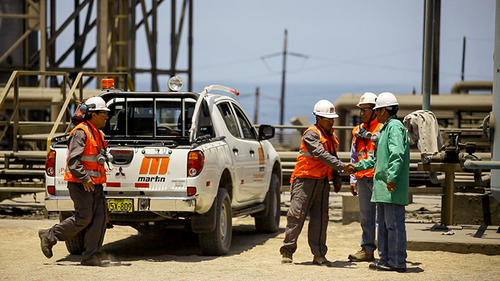
Free Engineering and Application Assistance
Our technicians have solved problems for people in your industry all over the world. Take advantage of our wealth of knowledge. Tell us about your situation today to learn how Martin can improve your performance, safety and bottom line - with no obligation. We want to ensure that you choose the right solution for your exact needs and we are willing to invest the time upfront to get it right the first time.
Contact Us Now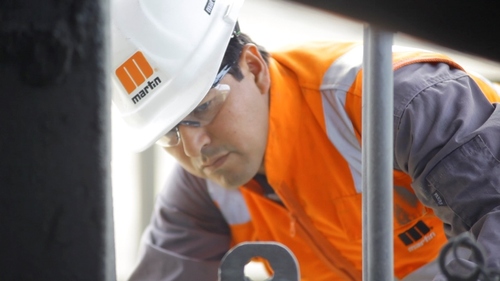
Save With Our Martin® Walk the Belt™ Service!
Every conveyor is different, even within the same facility! We can provide regularly-scheduled reviews of your bulk material handling system components, involving a specialized crew with the expertise necessary to achieve high operating standards, keeping the conveyor system running at maximum productivity. Immediate data and photos will be available to facility managers and our suggestions will ensure long-term savings and efficiency.
Get Your Belts Reviewed By People Who Know What They’re Looking At -- At No Charge!